В попытке рационализировать и оптимизировать операции по техническому обслуживанию, производственные и технологические организации активно внедряют программы обслуживания, ориентированные на надежность (RCM). Процесс RCM позволяет разрабатывать решения по распределению ресурсов, чтобы гарантировать прямую взаимосвязь между техническим обслуживанием и целями обеспечения надежности.
В свою очередь, цели надежности согласованы с целями организации, такими как максимизация прибыли и акционерного капитала, обеспечение безопасности, минимизация воздействия на окружающую среду и т. д. Это необходимо для оптимизации работы предприятия.
Важным инструментом RCM является анализ последствий отказов (FMEA). В отличие от анализа основных причин отказов (FRCA), который применяется для выявления отказов постфактум, FMEA — это систематический процесс, предназначенный для выявления возможных отказов и последствий до их возникновения.
На самом деле, FRCA и FMEA дополняют друг друга. FRCA позволяет подготовить почву для FMEA, а FMEA, в свою очередь, предусматривает создание плана по развертыванию соответствующих процедур обслуживания. Применение только лишь FRCA не дает должного результата, поскольку отказ происходит до применения процедуры, и это слишком дорого обходится в случае с критически важными системами.
Намного разумнее заблаговременно оценить вероятные отказы и их последствия либо смоделировать отказы в экспериментальной среде, чем допустить возникновение отказа до утверждения плана технического обслуживания.
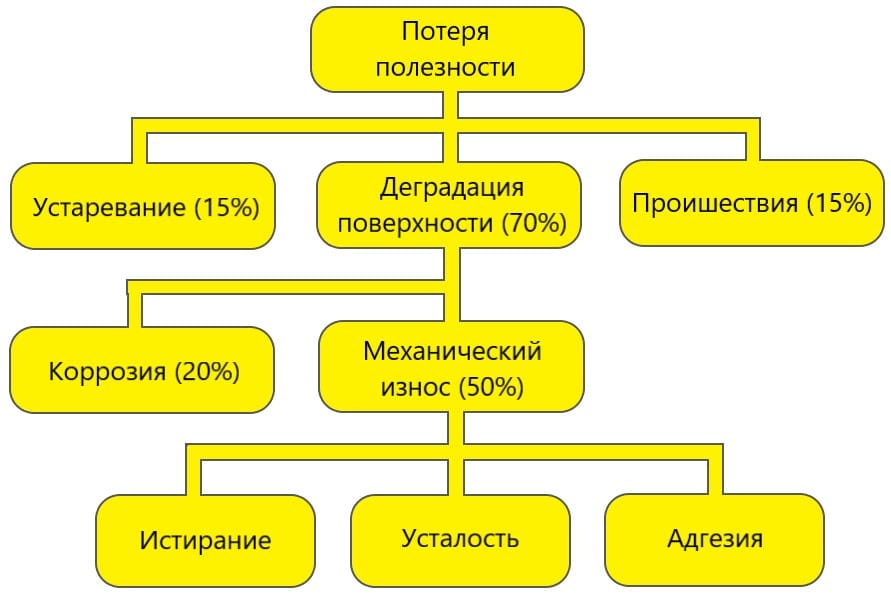
Заслуженный профессор Массачусетского технологического института Эрнест Рабиновиц в своей книге «Трение и износ материалов» говорит, что примерно в 70 % случаев, когда механическое оборудование теряет свою эффективность, изнашивается и подвергается коррозии, причиной является деградация поверхностей (см. рис. 1).
Отраслевые эксперты сходятся во мнении, что износ промышленного оборудования в 40–75 % случаев так или иначе связан со смазкой, и, следовательно, от 25 до 50 % всех случаев потери полезности оборудования происходят именно из-за неисправностей в системе смазки.
Несмотря на распространенность отказов, связанных со смазкой, они далеко не всегда должным образом документируются. Например, внезапное снижение объема масла, вызванное расшатыванием сливной пробки из-за вибрации, и добавление в систему несоответствующего масла могут классифицироваться как «сбой смазки». Хотя оба эти фактора могут значительно ухудшить смазывание, природа этих неисправностей совершенно разная.
Следует также отметить, что отказы системы смазки зачастую ошибочно диагностируются как «поломка подшипника», «неисправность насоса» и т. п., однако это лишь симптомы проблемы, а не ее причины. Даже если было установлено, что причиной отказа стала смазка, то по-прежнему неясно, что именно с ней не так, а без этой информации устранить неисправность куда сложнее. FMEA — превосходный инструмент предварительного анализа, который позволяет более точно выявлять неисправности смазки, а также прогнозировать сбои, планировать восстановление и формировать экономически эффективные стратегии технического обслуживания.
Процесс FMEA
FMEA — отнюдь не новая процедура. Однако она ранее не применялась для оптимизации обслуживания. Различные компоненты и этапы процесса FMEA при базовом обслуживании описаны ниже и показаны на рис. 2.
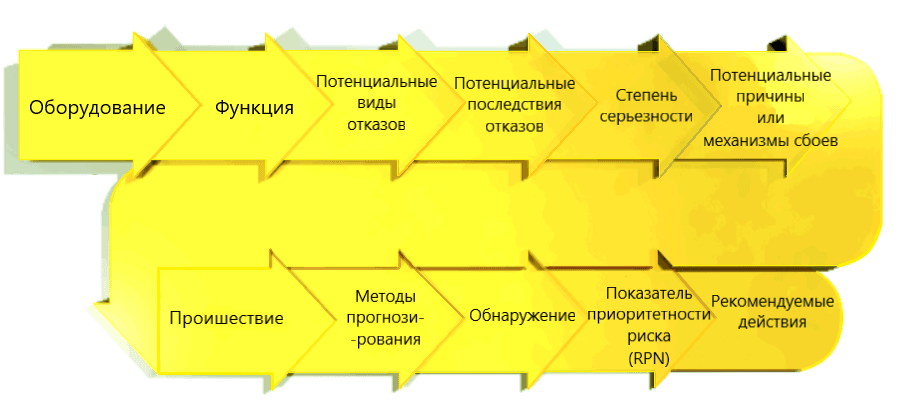
1. Составьте список оборудования на уровне системы и (или) подсистемы. Степень серьезности неисправности системы зависит от критичности ее функционирования. Обычно рекомендуется начинать с наиболее крупных узлов и по мере необходимости детализировать перечень при выполнении процедуры.
2. Определите функции, выполняемые оборудованием для достижения целей организации. Например, при штамповке гидравлический пресс (оборудование) должен штамповать материал (функция), чтобы организация могла достичь своих бизнес-целей.
3. Определите возможные режимы отказа. Отказ насоса — это одна из ситуаций (режимов), при которой гидравлический пресс может не выполнять свою заданную функцию. Как правило, на то чтобы отличить функциональные сбои от технических, уходит слишком много времени. Руководство зачастую не может прийти к единому мнению о причинах возникшего сбоя.
Предположим, что человек приобрел новый спортивный автомобиль с заявленной максимальной скоростью 150 миль в час. Посетив испытательный трек, счастливый владелец выясняет, что его автомобиль способен развивать скорость лишь 145 миль в час. Технически машина вышла из строя. С функциональной точки зрения он неисправен лишь в том случае, если движение со скоростью более 145 миль в час является обоснованным требованием для транспортного средства.
4. Перечислите возможные последствия отказа. Различные режимы отказа по-разному влияют на организацию. Если в гидравлическом насосе образовалась трещина, то он перестает работать совсем. Если насос износился с течением времени, что привело к снижению его объемного КПД, его работа может замедлиться или может потребоваться больше энергии для обеспечения такой же производительности, как у правильно работающего насоса.
5. Определите степень серьезности. Чтобы иметь возможность провести сравнительный анализ и расставить приоритеты, необходимо каждому происшествию присваивать степень серьезности отказа. Этот показатель отражает относительное влияние сбоя на работу предприятия с учетом стоимости простоя в час и его ожидаемой продолжительности, затрат на ремонт, затрат на лечение персонала, получившего травмы, затрат на устранение загрязнения окружающей среды и т. д. Серьезность отказа обычно оценивается по шкале от одного до десяти, где один балл — минимальное значение, а десять — наивысшая степень серьезности.
В каждой организации свое собственное понимание длительности простоя. Как правило, последовательные производственные линии более чувствительны к простоям, чем операции, в которых несколько машин выполняют одну и ту же функцию, а потеря одной машины приводит лишь к частичной потере производственной мощности.
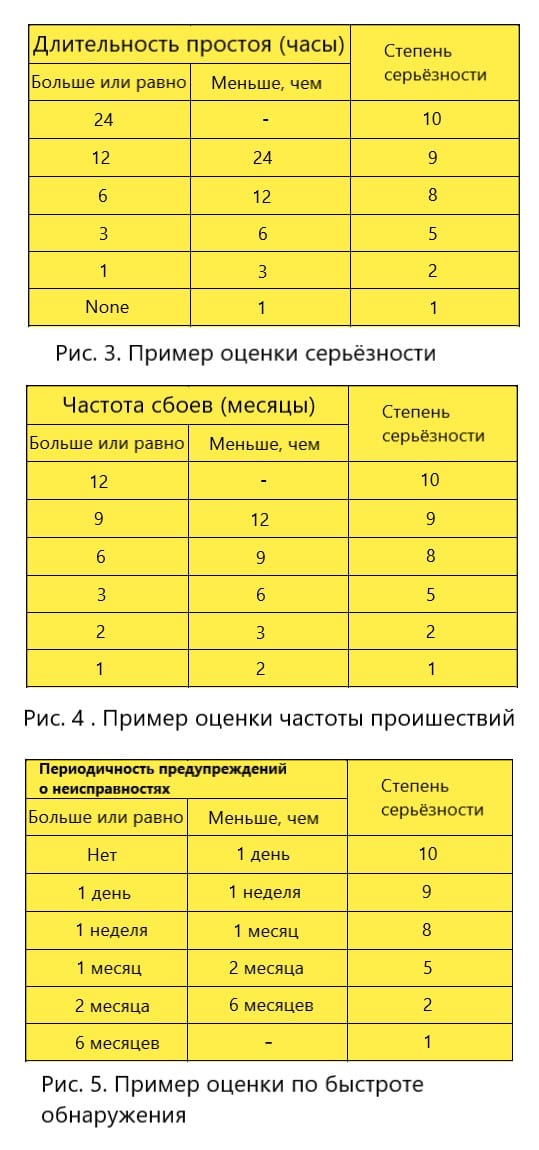
Серьезность каждого отказа можно определять различными способами, но в промышленной отрасли самым рентабельным оказался подход на основе усреднения. На рис. 3 показана степень серьезности, определяемая по продолжительности простоя в результате отказа.
6. Определите потенциальные механизмы отказа. Механизмы отказа, иногда называемые «вынуждающими функциями», объясняют, почему может возникнуть конкретный режим отказа или раскрывают его первопричины. Например, механизм кавитации может привести к режиму отказа «неисправность насоса», в результате чего может произойти остановка или замедление производства.
7. Укажите оценку частоты возникновения для каждого механизма отказа. Снова оцените по десятибалльной шкале периодичность (единица — наименее часто, десять — наиболее часто) возможного возникновения каждого механизма отказа. На рис. 4 показан пример системы, используемой для оценки частоты отказов.
8. Определите методы прогнозирования. Расширенные предупредительные меры снижают влияние сбоя на производство, позволяя руководству планировать простои, заранее готовить запчасти и расходные материалы, а также привлекать персонал с соответствующими навыками для выполнения восстановительных работ. Перечислите различные методы, с помощью которых можно обнаружить каждый сбой.
9. Задайте оценку быстроты обнаружения для каждого режима/механизма отказа. Снова по шкале от одного до десяти (единица — интервал времени больше, десять — интервал времени короче) оцените эффективность применяемых систем раннего предупреждения (например, анализа масла, анализа вибрации и т. д.). На рис. 5 представлен пример таблицы оценок, отражающих период заблаговременного предупреждения о неисправности.
10. Назначьте показатель приоритетности риска (RPN). RPN рассчитывается путем умножения оценки серьезности на оценку частоты происшествия и на оценку быстроты обнаружения (серьезность × происшествие × обнаружение = RPN). RPN оценивает важность каждого потенциального функционального отказа по шкале от одного до 1000, где единица — самый низкий приоритет, а 1000 — самый высокий.
Хотя этот метод является псевдоколичественным, он систематичен и эффективен для сравнения и расстановки приоритетов. Поскольку он основан на входных значениях, полученных методом усреднения, производное значение RPN также основано на усреднении.
11. Определите рекомендуемые действия по техническому обслуживанию. Рекомендации зависят от характера и серьезности различных режимов и механизмов отказа, стоимости развертывания методов и технологий обнаружения, а также RPN. Здесь могут быть указаны различные элементы от модификации оборудования до процедур проверки.
Процедура FMEA в области смазки
В большинстве случаев при работе с механическими системами инженер по надежности должен воспринимать смазочный материал как критический компонент системы, так как в данном случае не существует резервной или запасной системы для выполняемой смазочным материалом функции, если только не предусмотрена резервная машина в сборе.
Аналогичным образом отказ смазки может привести к значительному вторичному повреждению других компонентов системы. Ввиду критической важности смазочного материала и распространенности механических отказов из-за системы смазки, термин «отказ смазки» должен быть более точно определен в процессе FMEA, чтобы реализовать все преимущества RCM.
Процесс FMEA для системы смазки начинается с оценки функций смазочного материала в отношении каждого элемента оборудования в рамках рассматриваемой системы, а также оценки механизмов отказа, которые могут препятствовать эффективному смазыванию. С помощью таблицы на рис. 7 выполните следующую процедуру.
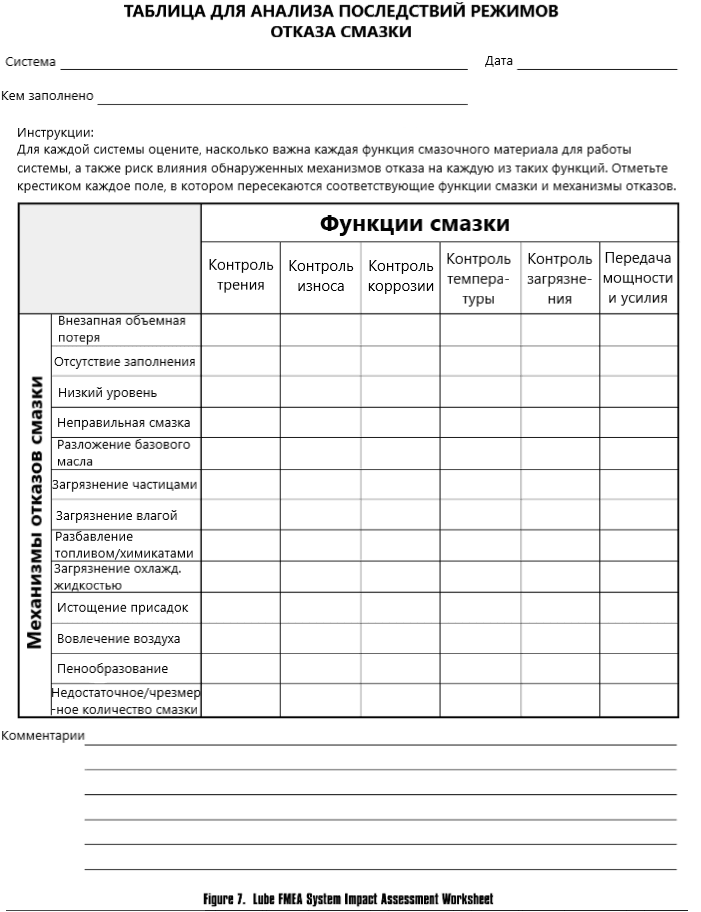
1. Определите функции, которые смазочный материал должен выполнять для каждой рассматриваемой машины.
2. Определите механизм отказа, связанный со смазкой, который может препятствовать работе машины.
3. Поставьте «X» в тех полях, где функция смазки и механизм отказа смазки пересекаются для данной машины. Например, деградация смазочного материала не может ухудшить передачу усилия в системе смазки подшипника, так как эта функция характерна для гидравлических машин.
4. В разделе «Причины» или «Механизмы отказа» укажите конкретные отказы, связанные со смазкой, которые являются первопричинами режимов отказа, приводящих к потере функциональности системы. Например, механизм отказа системы смазки «потеря мощности и передачи усилия из-за загрязнения частицами» может привести к полной или частичной потере производительности гидравлической системы (режим отказа), в результате чего машина прекратит штамповку, формовку и т. п.
5. Завершите процедуру FMEA в соответствии с приведенными выше инструкциями.
Заключение
Таблица FMEA для смазочных материалов представляет собой инструмент, позволяющий специалисту по смазке точно и в соответствии с процедурой FMEA определять отказы, связанные со смазкой, учитывая при этом функцию машины и влияние на достижение бизнес-целей компании.
Отказавшись от бессистемного отнесения технически не связанных отказов к категории «отказ смазки», можно добиться более высокой точности обслуживания и эффективности контроля основных первопричин отказов. Похожая методика может использоваться и в дедуктивном процессе FRCA, чтобы эффективнее определять уже возникшие отказы смазки.
- Автор статьи:Дрю Тройер
- Источник:FMEA Process for Lubrication Failures
- Использованная литература:1) Мубрей, Дж. (1997 г.) «Обслуживание, ориентированное на надежность», второе издание, Industrial Press Inc., Нью-Йорк
2) Рабиновиц, Э. (1995 г.) «Трение и износ материалов», второе издание, John Wiley & Sons, Нью-Йорк
3) Котнареану, Т. (1999) «Старые инструменты – новое применение: процедура FMEA для оборудования», издание «Прогресс качества», декабрь, стр. 48-52